Comprehending What is Porosity in Welding: Reasons and Solutions
Wiki Article
The Science Behind Porosity: A Comprehensive Guide for Welders and Fabricators
Recognizing the detailed systems behind porosity in welding is essential for welders and makers pursuing impeccable workmanship. As metalworkers look into the midsts of this sensation, they uncover a world governed by numerous factors that influence the formation of these tiny gaps within welds. From the structure of the base products to the details of the welding procedure itself, a wide variety of variables conspire to either exacerbate or reduce the existence of porosity. In this detailed overview, we will decipher the science behind porosity, discovering its effects on weld high quality and unveiling advanced techniques for its control. Join us on this journey through the microcosm of welding blemishes, where accuracy meets understanding in the quest of remarkable welds.Comprehending Porosity in Welding
FIRST SENTENCE:
Exam of porosity in welding exposes crucial understandings into the stability and top quality of the weld joint. Porosity, identified by the presence of tooth cavities or spaces within the weld steel, is a typical issue in welding procedures. These voids, if not correctly dealt with, can jeopardize the structural integrity and mechanical residential properties of the weld, causing prospective failings in the ended up product.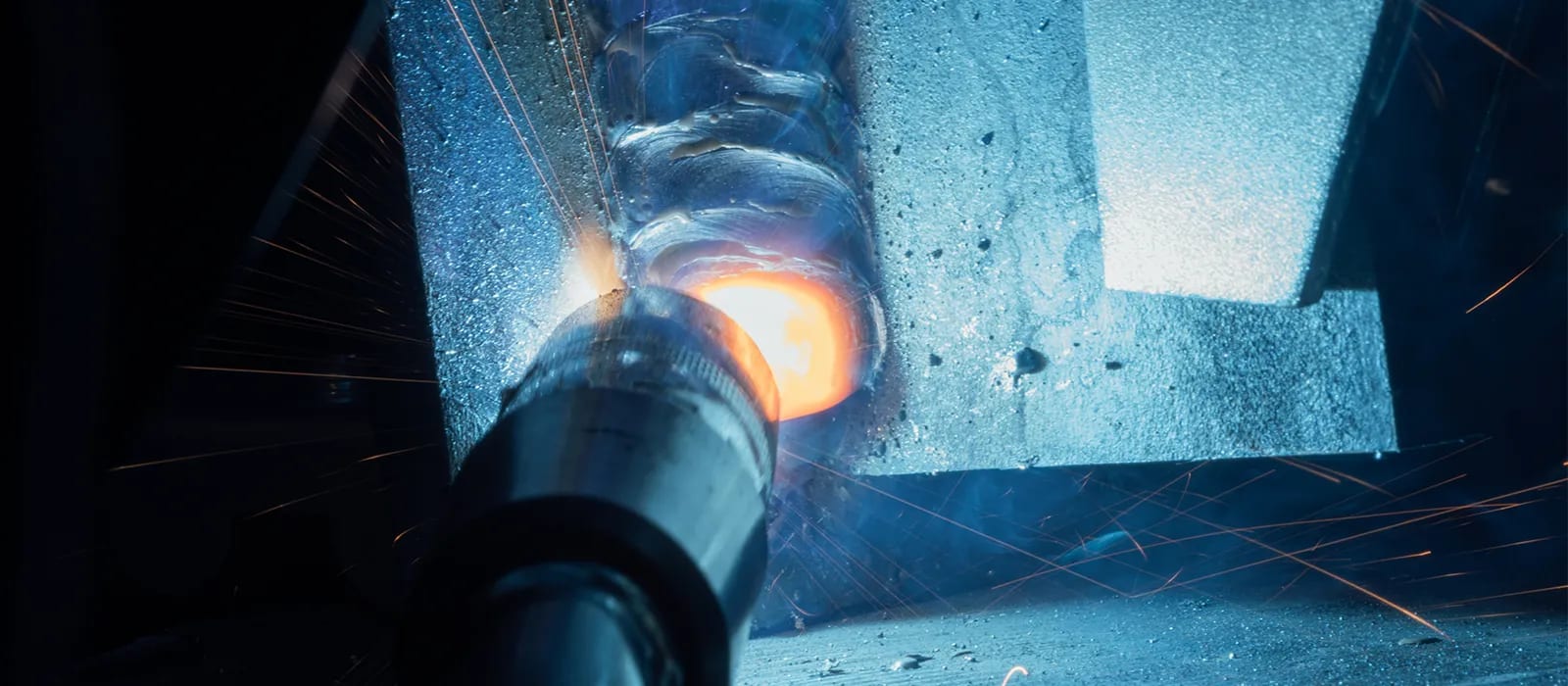
To identify and evaluate porosity, non-destructive screening approaches such as ultrasonic testing or X-ray examination are often employed. These methods allow for the identification of inner flaws without jeopardizing the honesty of the weld. By analyzing the size, shape, and distribution of porosity within a weld, welders can make informed choices to enhance their welding procedures and attain sounder weld joints.
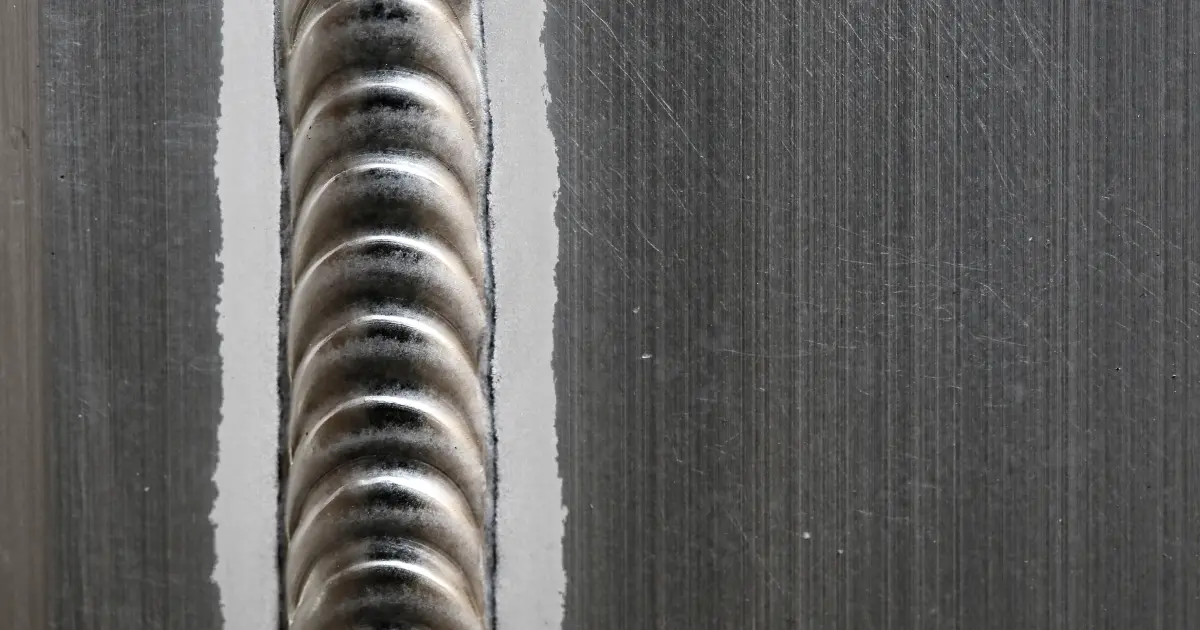
Elements Affecting Porosity Development
The incident of porosity in welding is influenced by a myriad of aspects, varying from gas protecting performance to the details of welding parameter settings. Welding specifications, consisting of voltage, existing, take a trip speed, and electrode type, additionally influence porosity development. The welding method employed, such as gas metal arc welding (GMAW) or secured steel arc welding (SMAW), can affect porosity development due to variants in warmth circulation and gas insurance coverage - What is Porosity.Effects of Porosity on Weld Top Quality
Porosity development significantly compromises the architectural honesty and mechanical properties of welded joints. When porosity is existing in a weld, it produces gaps or tooth cavities within the material, lowering the overall toughness of the joint. These voids serve as stress and anxiety focus factors, making the weld extra vulnerable to breaking and failure under lots. The existence of porosity also damages the weld's resistance to rust, as the trapped air or gases within the spaces can react with the surrounding atmosphere, bring about destruction with time. Furthermore, porosity can prevent the weld's capability to endure stress or effect, additional jeopardizing try this out the general quality and dependability of the welded structure. In important applications such as aerospace, vehicle, or architectural building you can try this out and constructions, where security and longevity are critical, the harmful results of porosity on weld high quality can have serious repercussions, stressing the importance of minimizing porosity via proper welding techniques and treatments.Methods to Minimize Porosity
Furthermore, making use of the appropriate welding parameters, such as the correct voltage, current, and take a trip speed, is critical in protecting against porosity. Keeping a constant arc size and angle during welding also assists lower the probability of porosity.
Using the proper welding technique, such as back-stepping or employing a weaving motion, can additionally assist disperse heat equally and lower the possibilities of porosity development. By carrying out these strategies, welders can efficiently reduce porosity and create high-quality bonded joints.

Advanced Solutions for Porosity Control
Implementing innovative innovations and innovative methods plays a critical duty in achieving premium control over porosity in welding processes. One sophisticated solution is using sophisticated gas combinations. Protecting gases like helium or a mix of argon and hydrogen can assist decrease porosity by offering far better arc stability and boosted gas protection. Additionally, using innovative welding strategies such as pulsed MIG welding or changed ambience welding can additionally help mitigate porosity issues.One more innovative solution includes the use of innovative welding tools. As an example, making use of devices with built-in functions like waveform control and sophisticated power sources can boost weld top quality and lower porosity dangers. The execution view publisher site of automated welding systems with accurate control over criteria can substantially reduce porosity issues.
In addition, incorporating advanced tracking and evaluation technologies such as real-time X-ray imaging or automated ultrasonic screening can help in finding porosity early in the welding procedure, enabling immediate restorative actions. In general, integrating these sophisticated options can considerably improve porosity control and improve the total top quality of welded parts.
Conclusion
In verdict, recognizing the science behind porosity in welding is necessary for welders and producers to create high-grade welds. By determining the elements affecting porosity development and applying strategies to decrease it, welders can boost the general weld high quality. Advanced solutions for porosity control can better boost the welding procedure and make certain a strong and trustworthy weld. It is very important for welders to constantly enlighten themselves on porosity and implement best practices to achieve ideal outcomes.Report this wiki page